With a skills shortage in the manufacturing industry, WLR Precision Engineering Ltd. had a burning desire to automate its high-precision production while maintaining the skill levels of its highly qualified team of engineers.
The opportunity to increase throughput, precision, quality and consistency prompted the Wilford-based subcontractor to purchase a 5-axis Kern Micro Vario machining centre with an Erowa Compact 80 automated pallet loading system from Rainford Precision.
Located just south of Nottingham, WLR undertakes everything from prototype work to small and medium batches for manufacturers in the oil exploration, medical and pharmaceutical sectors, to name a few. As a company ‘dedicated to precision’, the ISO: 9001:2015 certified manufacturer is already an existing Kern user, reaping the rewards of unparalleled precision and performance. In 2013, WLR installed a Pyramid Nano machining centre.
Discussing why WLR invested in its second Kern machine, the automated Kern Micro Vario, Kevin Callon, Managing Director at WLR, said: “One of my regrets was not having some form of automation on the Pyramid Nano when we first bought it, despite having the option. There was no way we would have bought another Kern without some form of automated loading to maximise the running hours of the machine.”
Based on the precision of the Pyramid Nano, this regret was founded upon the realisation that the company needed extremely precise machining capacity for a range of higher quantity runs of extremely accurate components. With an 80-component Erowa pallet loading system and a 90-position automatic tool change, the Kern Micro Vario was the perfect solution.
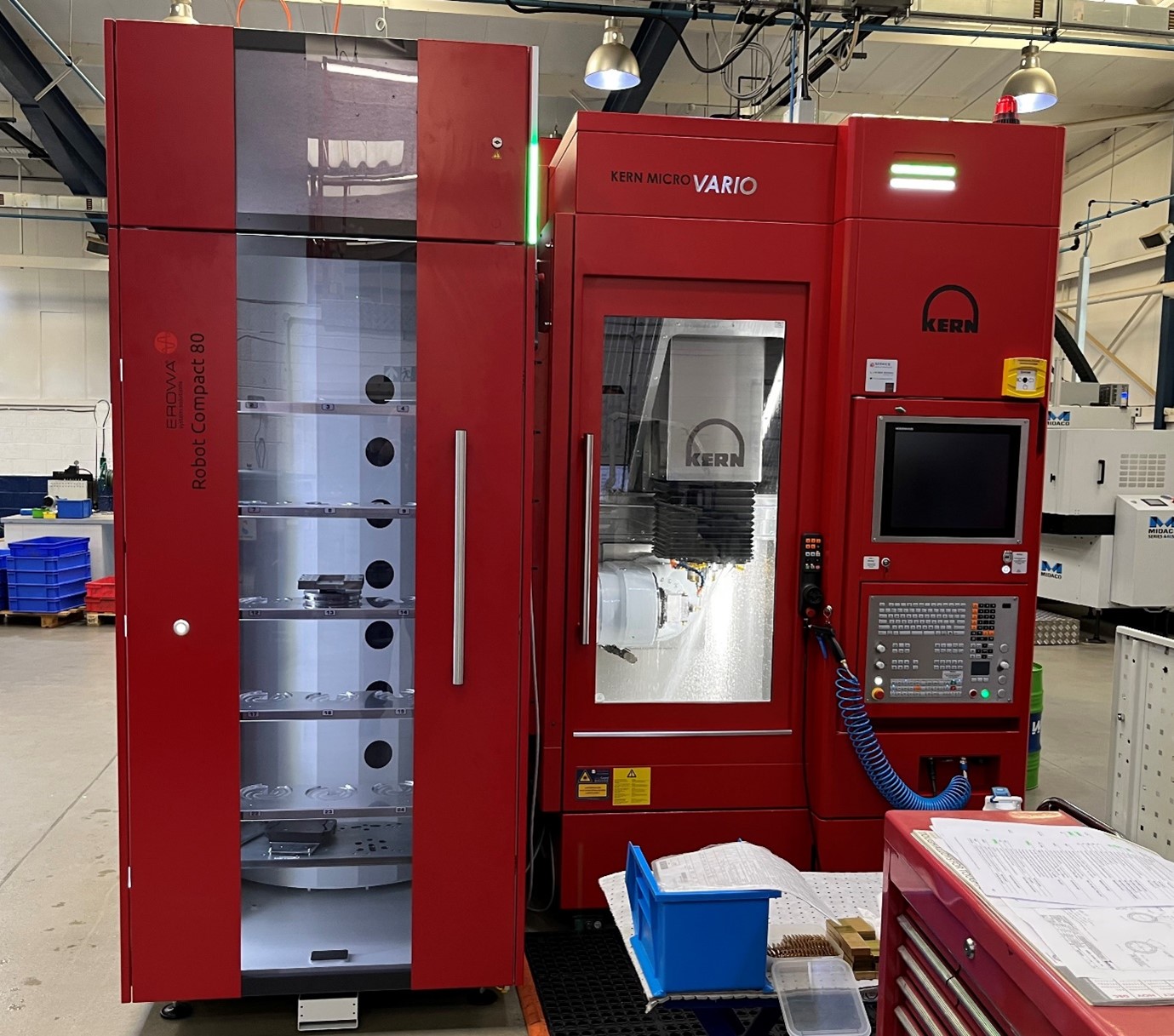
Installed in September 2022, the introduction of the automated Micro Vario now enables WLR to run production continuously ‘lights-out’ whilst utilising the existing Pyramid Nano for smaller batch runs and one-offs during daytime working hours.
Kevin explained: “The consistency of the components produced on the new Kern is amazing and repeatable to the micron. The precision is so impeccable that we now channel as much work as possible through the Kern Micro Vario. It’s not only doing the really demanding high-accuracy work that it was purchased for but also undertaking the less demanding work that would normally be done on less precise machining centres.”
With incredible accuracy and repeatability, the engineering team’s demand to constantly check that workpieces are within tolerance and conform to requirements is reduced. This alleviates pressure from the inspection team, which can rest assured that the precision levels achieved by the Kern are repeatable to the micron on the Kern.
The Kern Micro Vario precision and repeatability is built upon the foundations of its thermally stable Ultra-High-Performance Concrete (UHPC) base and internal temperature management system that combine with unrivalled kinematics and sophisticated design to yield precision and repeatability of <1.5µm and <1µm respectively. From a specification perspective, the Kern Micro Vario has a compact X, Y, and Z-axis work envelope of 350 by 220 by 250mm, a -110° to +110° swivelling B-axis, and a 360° continuous C-axis.
The tool changeover is less than 3 seconds, and the chip-to-chip time is 4.5 seconds – all feeding a high-speed 42,000rpm HSK 40 spindle. Incorporating the powerful Heidenhain TNC640 CNC control, 30m/min rapid rates and acceleration of 10 m/s², the Micro Vario demonstrates astounding flexibility, speed and precision in a compact floor area.
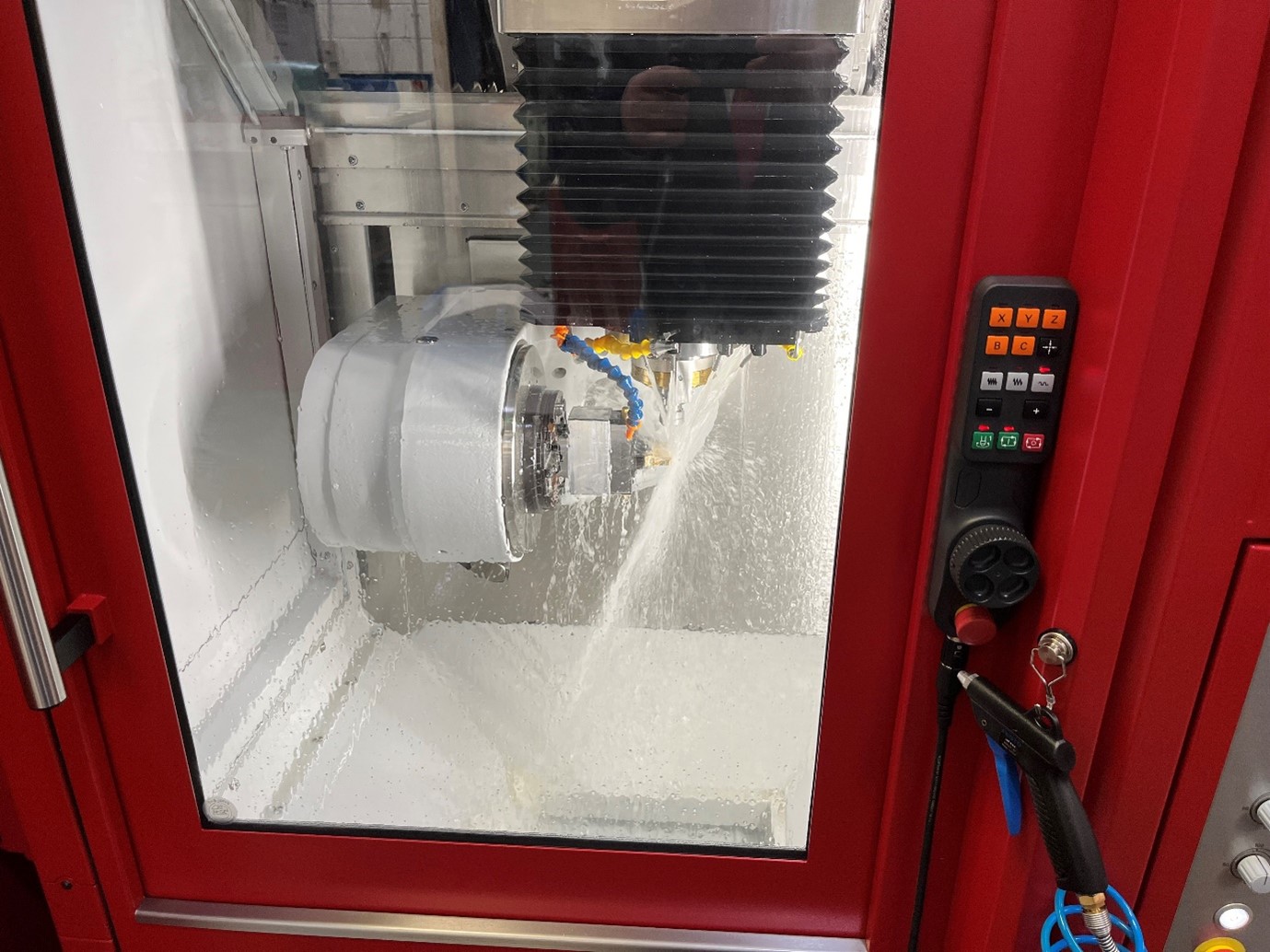
Highlighting what distinguishes the Kern from other machine tools the company uses, Kevin states:
“It’s definitely the accuracy and repeatability. There’s also a significant improvement in surface finishes. The Kern truly excels, particularly with harder materials. This excellence isn’t solely due to spindle concentricity but rather the entire package. It’s a very robust machine engineered to deliver remarkable repeatability.” Kevin added: “Previously, we didn’t have enough of the right kind of work for the Kern to keep it fully occupied. We began assigning other tasks to the machine to utilise its capacity. We now appreciate the advantages of this approach, given its repeatability. The tolerances we find difficult to maintain on other machines are effortlessly attained on the Kern. This level of precision and repeatability optimises operations further downstream in our business.”
With machine utilisation down to a ‘fine art’ and the variation in size and complexity of components in the workpiece loader honed to perfection, the company founded in 1969 is maximising the capabilities of the Kern.
Kevin stated: “The cost benefits are considerable as we never scrap anything. When we run the machine unmanned through the night, we know that everything will be spot on when we come in the next day.”
Even amongst the extremely impressive array of CNC machine tools at WLR, the Kern Micro Vario was a complete game changer regarding repeatability and consistent part quality. In these demanding times, the ability to produce consistently high quality is key to ensuring complete customer satisfaction, and it certainly looks as if WLR has found the right solution.
Alluding to the Kern machine’s cost per part, Kevin continues:
“Based on cost per part, the machine more than pays for itself. It completes jobs in one hit, faster and easier than other machines, and to tighter tolerances. As we have such robust processes in place, it has generally reduced the burden on the inspection department and the workforce. It has also improved planning and lead times because parts come off the machine ‘right first time’. Overall, it is a great asset to our business.”