A TruPrint 3000 metal additive manufacturing (AM) system from TRUMPF has been acquired by the Manufacturing Technology Centre (MTC). Installed within the MTC’s National Centre of Additive Manufacturing (NCAM), this advanced machine, which is based on laser metal fusion (LMF) technology, forms a key part of the NCAM capability.
Established in 2010, the Coventry-based MTC is an independent research and technology organisation (RTO) with the objective of bridging the gap between academia and industry. The MTC provides integrated manufacturing system solutions for customers large and small, across sectors as diverse as automotive, aerospace, rail, informatics, food & drink, construction/civil engineering, electronics, oil and gas and defence.
The MTC also hosts NCAM, which accelerates the uptake of AM by developing the technology and systems required to address the key challenges within the AM value chain. NCAM is the instigator of the DRAMA project (Digital Reconfiguration Additive Manufacturing facilities for Aerospace), a three-year, £14.3 million collaborative research project) which in turn forms part of the UK’s Aerospace Technology Institute’s programme; started November 2017.
As a Tier-2 member, TRUMPF works closely with the MTC and supports the overall objectives of NCAM. Helping to further this ambition – as part of a major expansion in capability – NCAM identified and acquired the TRUMPF TruPrint 3000 metal AM system.
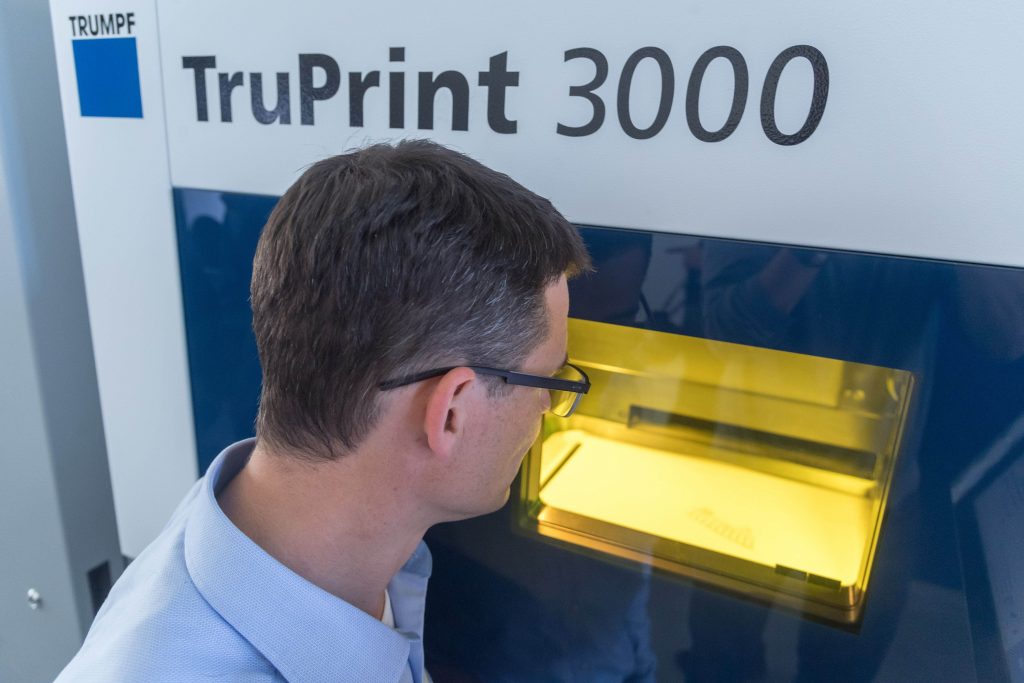
The machine has been located in NCAM’s recently opened (15 October) innovation and knowledge hub for metal AM. In a significant advance for the UK, the new hub aims to lead research, development and collaboration in metal AM, developing and testing ideas for taking the technology forward.
The hub, among the first of its type in Europe, underscores progress in the DRAMA project, and includes a workshop, as well as design, research and test facilities for AM users and experts who can shape the technology.
“The idea behind installing the TRUMPF TruPrint 3000 is to showcase laser powder bed technology,” explains Ross Trepleton, Chief Engineer at the MTC. “Our new innovation and knowledge hub for metal AM has only been open since October, but already we have a range of different AM platforms in place, the latest of which is the TruPrint 3000. We’re trying to demonstrate to industry the fundamental differences between the various AM technologies available on the market.”
TRUMPF’s TruPrint 3000 is a universal medium-format machine with industrial part and powder management that is designed for the series production of complex metal components. Parts can be flexibly arranged in the generous build area, which measures 300 mm in diameter by 400 mm in height.
“The addition of the TruPrint 3000 is nice because the machine is very productionised,” says Mr Trepleton. “For instance, build and supply cylinders can be quickly replaced, which allows users to reduce set-up times and increase productivity and machine utilisation rate. Furthermore, the machine’s engineered structure is very robust.”
The TruPrint 3000 is fitted with a TRUMPF 500 W fibre laser offering a wavelength of 1,070 nm. Notably, the focal diameter, which can be individually adjusted between 100 and 500 μm, makes it possible to react very flexibly to various component requirements. Layer thickness lies between 20-150 µm to produce even more detailed workpieces.
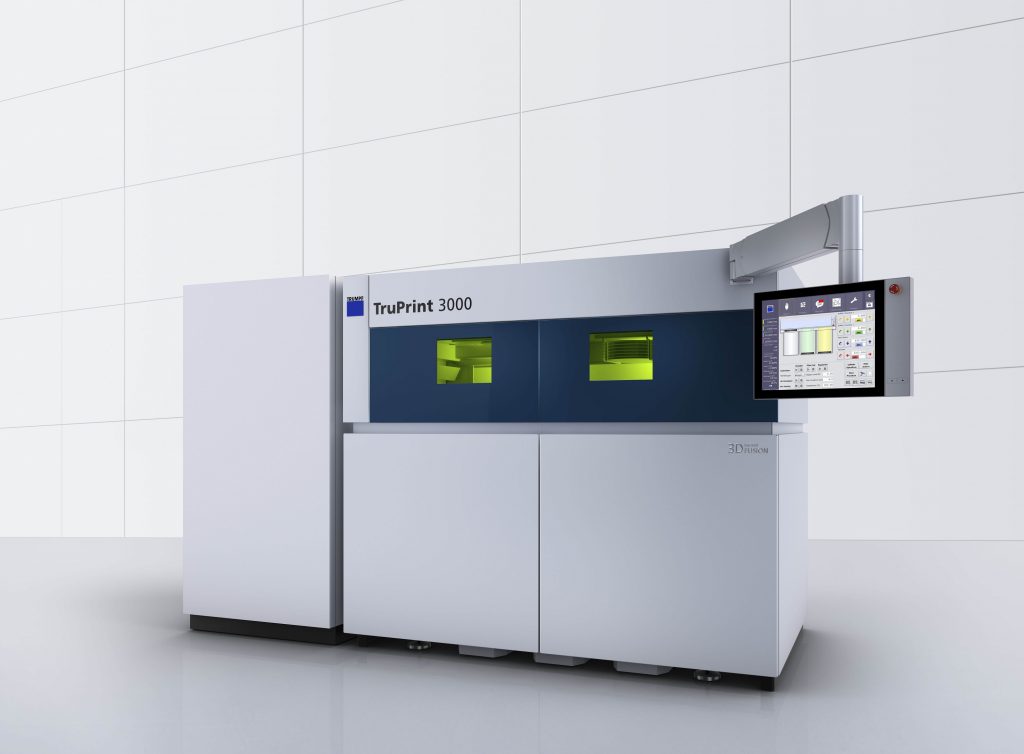
“With machine commissioning and training complete, the TruPrint 3000 is available to any company that has an interest in metal AM,” says Mr Trepleton. “We have deliberately invested in high-end systems for each type of metal AM platform, to see how the technologies compare with each other. Those coming to use the machines will soon discover which works best for their particular application, ultimately helping to guide their investment decisions.”