Siemens Congleton and Sudbury facilities in action to fight Covid-19
Every ventilator made can save a life
The gravity of the Covid-19 challenge has been made clear by the UK Government. The National Health Service needs thousands of ventilators and UK industry has been asked to respond to the challenge.
Siemens UK and Siemens Healthineers are part of the VentilatorChallengeUK consortium, alongside businesses from the automotive, aerospace and technology sectors to respond to this urgent challenge.
Brian Holliday, UK Managing Director, Siemens Digital Industries said:
“Siemens Healthineers has vital expertise in manufacturing medical devices in the UK and Siemens Digital Industries has expertise in making manufacturing processes more efficient and highly productive. Together these parts of the company are combining their efforts to contribute to the Ventilator Challenge. We are so motivated to work together with other companies to help the NHS as every ventilator made can save a life.”
Ali Burns, Managing Director of the Siemens Healthineers Sudbury business who is project managing for Siemens UK and Siemens Healthineers, said:
“Siemens does not manufacture ventilator products itself, but as a company we have expertise in healthcare manufacturing and manufacturing productivity technology which will, alongside the efforts of the other consortium members, help the companies who do make these products to massively ramp up the production to meet the levels required.”
Specifically, Siemens is providing expert assistance to the consortium in medical device manufacture under the standards to MHRA guidelines, mainly through the team at Siemens Healthineers facility in Sudbury. This is being carried out in addition to, and without disruption to, existing demand for blood gas analyser products which are also massively in demand and a crucial part of the fight against Covid-19.
Siemens Healthineers is advising the coalition on post final assembly testing and has valuable programme management experience in the UK healthcare environment, helping to ensure strict regulation requirements are factored in from the start and that vital time is not lost in the highly accelerated production process.
Siemens Industry Software has enabled the consortium to rapidly distribute bills of materials, quality work aids and to design, simulate and test the scaled-up manufacturing locations. Engineers from across Siemens UK have been working to capture product and production models, simulate scaled manufacture and provide assembly workers with digital aids for sub-assemblies.
The collaboration at Siemens went further as colleagues from the gas turbine manufacturing and service plants in Lincoln took on the challenge to quickly convert complex drawings, source materials and machine additional fixtures which will aid the absorber assembly, all within three days.
Brian Holliday continued:
“Our manufacturing expertise from Siemens Digital Industries in Congleton is helping to accelerate the design of a new factory layout for one of the sub-assemblies of the Penlon ventilator. There is also further potential for Siemens to help through our Additive Manufacturing Network to 3D print metal parts through Siemens Materials Solutions in Worcester where we have a number of printing machines that use the laser powderbed fusion process.”
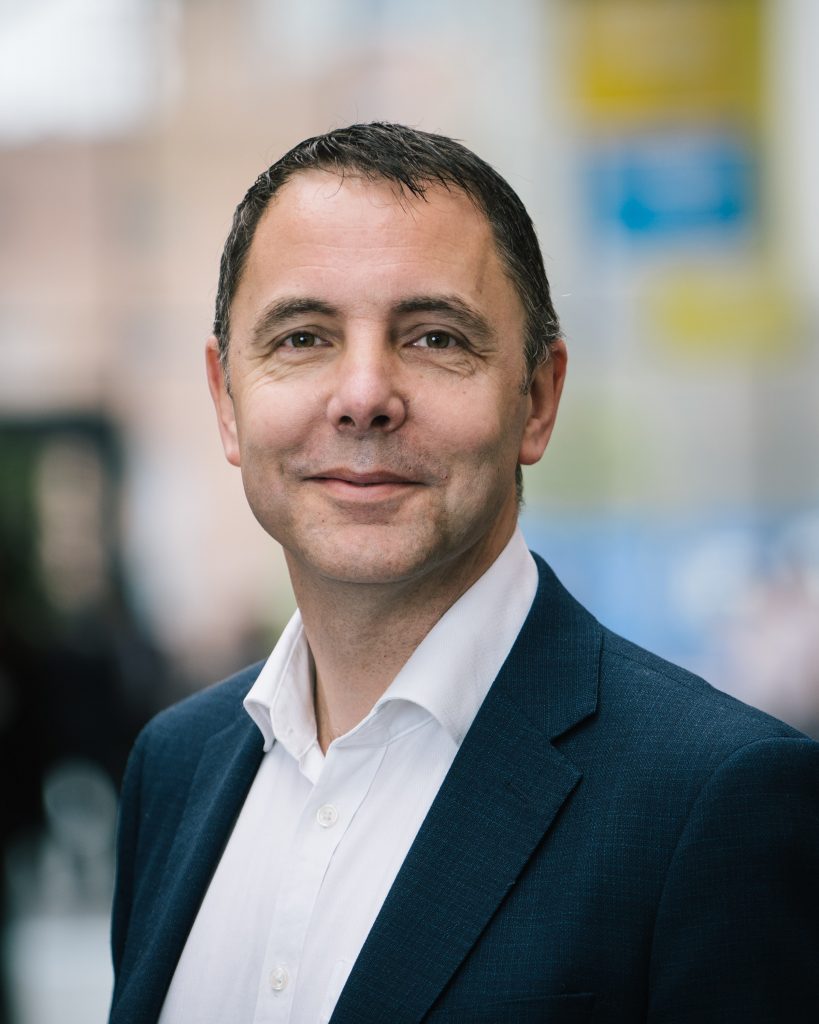