RARUK Automation has supplied a Universal Robots UR10 collaborative robot (cobot) to BWI Group’s Luton plant, which specialises in the assembly of complete suspension modules to the global transportation market. The UR10 is currently employed tending a blow-moulding machine, where completed parts are extracted every 25 seconds and placed in containers ready for shipping, saving on the need – and cost – of having a human operative in attendance.
With origins that can be traced back to the early 1900s, BWI Group is today a full service supplier of chassis, suspension and brake products. The company has partnerships with many blue-chip OEMs, including JLR, Porsche and Honda, and has a proven ability to manage tier-two and tier-three suppliers to ensure the just-in-time (JIT) delivery of modules.
At Luton, some 200 people help ensure production throughput matches demand. Of course, one way to simplify the task of meeting productivity targets, is to invest in automation.
“We did quite an extensive market study before acquiring our first robot,” explains Mike Hathway, Industrial Engineer at BWI Group in Luton. “We invited almost every UK supplier of robot technology to pitch at our facility. However, while this process was ongoing, I attended an automation workshop at JLR, where I happened to see a Universal Robots UR5 cobot in action. We hadn’t given much consideration to cobots until then, but everyone was really impressed, including me.” BWI Group duly invested in a UR10 model with 10 kg payload to suit a number of applications the company had in mind.
“First of all we put the UR10 to work tending a crimping machine,” says Mr Hathway. “The machine crimps outer canisters for air-suspension modules. To explain further, outside the flexible sleeve/bag that traps the air, there is a cylinder to help prevent over-expansion and punctures. The machine crimps the cylinder on to the bag, with the UR10 moving parts between each stage of the process: pre-check, crimp and after-check. There is one part in each station at any one time to provide continuous flow.” Previously this entire operation was manual, with a BWI Group employee performing all tasks.
Not long after the cobot was installed, an internal change of strategy saw the manufacture of these outer canisters relocated to another BWI plant in central Europe, so the UR10 was re-assigned to a different machine.
“UR-series cobots are extremely flexible and can be adapted to a whole host of applications, so we had no trouble finding another role for it,” says Mr Hathway. “We moved the UR10 to a blow-moulding machine, where it extracts dust covers every 25 seconds and loads them neatly into a container ready for shipment to another plant. Previously, the parts would just exit the machine and land randomly on a conveyor, which although a bit messy was fine when we used the dust covers in-house. However, the dust covers are now sent to another facility for assembly, so shipping them in a tangled, random way would render them unusable. If we didn’t deploy the UR10 here we would need a full-time operative at the end of the machine to pack the parts neatly. This job would be particularly dull, comprising five seconds of work and 20 seconds of waiting – hardly an efficient or cost-effective use of labour.”
“We’ve been nothing but impressed with our UR10,” says Mr Hathway. “Aside from the flexibility and reliability, the collaborative capability means we don’t need guarding and can create a far more compact cell – with due care relating to speeds, motion and grippers. Our factory is highly utilised and we don’t have sufficient space to be adding large guarded robot cells. Guarding also adds to the cost of a project. We are now looking at introducing further cobots and have a particular interest in the larger UR16.”
Another point of note highlighted is the support provided by RARUK Automation.
“The company helped in the early project stages, particularly with proof-of-concept, and in addition they are always on hand if I have a question about programming.” Mr Hathway concludes.
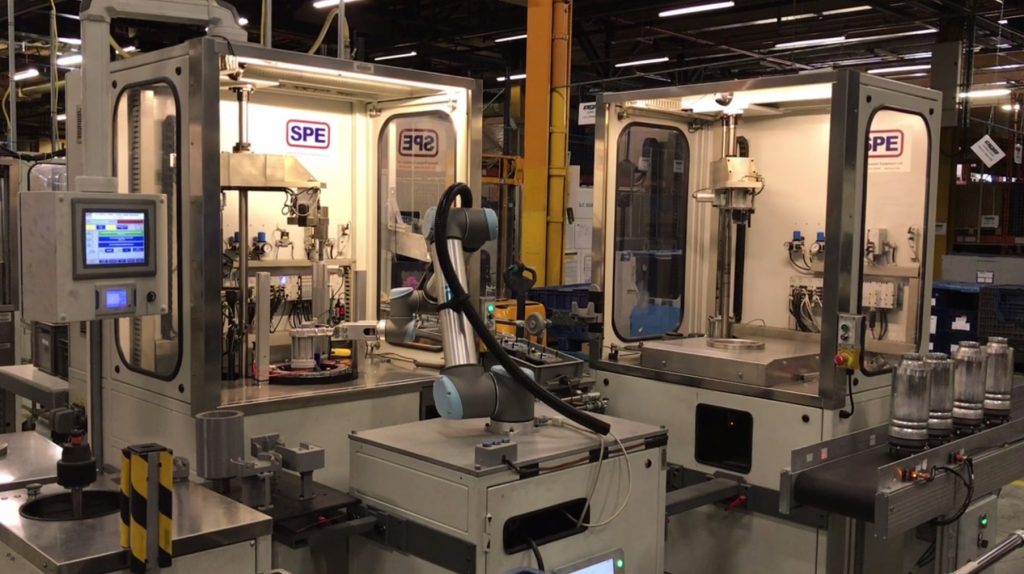
As a final aside, BWI Group is currently in the process of creating a new business venture, Open Automation, that will semi-integrate UR cobots on a stand complete with PLC and program, ready to sell to other end users. This venture will tap into the full range of Universal Robots available from RARUK Automation.