High-precision and high-performance milling and turning are two natural topics that visitors to the OPEN MIND booth can expect to see at MACH 2020 (Stand 440 Hall 17). However, at this years’ event, the industry leading CAD/CAM vendor will also provide manufacturers an opportunity to witness the unparalleled steps that hyperMILL® has taken with its latest release, Version 2020.1.
The latest hyperMILL® 2020.1 release introduces a raft of new features that include significant enhancements to everything from Slot-Rib Probing, 3D Optimised Roughing, 3D Profile Finishing, 3D and 5-axis Corner Rest Machining, 5-axis Blade Tangent Milling, ADDITIVE Manufacturing and Automatic Contour Feature Splitting. In addition to this, OPEN MIND has incorporated further improvements to the Settings Wizard, Toolpath Display, 5-axis Tube Finishing and 5-axis Contouring functions with more feature enhancements also incorporated into the hyperCAD-S® CAD platform.
The major new features in the latest hyperMILL® 2020.1 release arrive from the NC code-based hyperMILL® VIRTUAL Machining simulation solution, the Digital Twin concept and the hyperMILL® AUTOMATION Center.
Creating a perfect fusion between the virtual and real world, hyperMILL® VIRTUAL Machining creates a virtual representation of the actual machine tool.
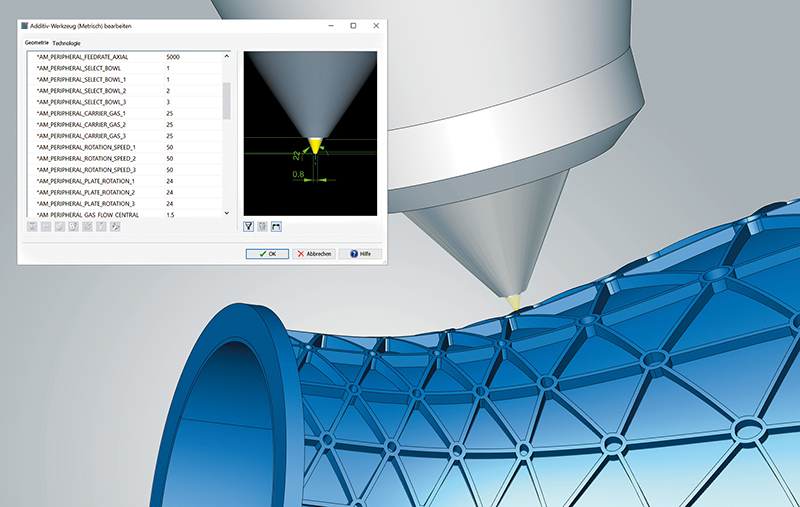
Virtual World With Real-World Benefits
In the modern manufacturing environment, the ability to create a virtual representation or ‘Digital Twin‘ of a machine tool is becoming increasingly important. Recognised as the only way to create simulations true to reality, hyperMILL® VIRTUAL Machining makes it possible to design a significantly more efficient and safer set-up. The confidence this instils in customers, especially when undertaking particularly complex work is truly invaluable.
hyperMILL®VIRTUAL
Machining consists of three modules
In the ‘Center‘, which is the simulation solution, the machine, the controller and PLC, are represented virtually and simulated based on the NC code – for maximum safety.
During the postprocessor run, the ‘Optimizer‘ automatically selects the best solution for collision-free orientation. In Version 2020.1, the Optimizer has been enhanced, so the automatic solution selection and calculation time during post-processor have been improved. This significantly reduces auxilliary processing times. The new ‘Smooth linking’ function automatically optimises all linking movements between the individual operations during the postprocessor run. This ensures that repositioning and movement is always in close proximity to the workpiece and checked for collisions. Subsequently the ‘CONNECTED Machining‘ feature enables bi-directional networking with the machine so that parameters can be compared against the CAM programme, and the machine can also be controlled remotely.
hyperMILL® Adds-up With Enhanced AM Features
Also reaching prominence in the modern manufacturing arena is Additive Manufacturing and OPEN MIND is geared-up for this with the latest hyperMILL® ADDITIVE Manufacturing updates in Version 2020.1.
hyperMILL® ADDITIVE Manufacturing allows manufacturers to perfectly control both additive and subtractive processes. For Powder Bed Fusion (PBF) OPEN MIND optimally integrates into the process chain to post-process printed parts. hyperMILL® ADDITIVE Manufacturing actively controls the material application of the Directed Energy Deposition (DED) process to ensure optimal results. In hybrid manufacturing processes that combine additive and subtractive manufacturing, hyperMILL® enables users to perfectly program additive layering and subtractive milling together. The unique 5-axis technology from OPEN MIND is ideal for simultaneously controlling 5-axis material deposition and thereby achieving optimal results. hyperMILL® ADDITIVE Manufacturing is the perfect partner for your additive manufacturing needs.
For
further information on the latest hyperMILL® 2020.1 release
and the updates to the hyperMILL® VIRTUAL Machining, hyperMILL®
AUTOMATION Center and the hyperMILL® ADDITIVE Manufacturing
modules, please visit the OPEN MIND Technologies Stand 440 in
Hall 17.