Cheetahs are famed for their ability to reach high speeds, but it is in fact their agility that is truly impressive. Cheetahs can accelerate from zero to 60 miles per hour in just three seconds, and then quickly decelerate, turn, and sprint in another direction. But this exceptional combination of speed and precision doesn’t purely belong to the wild, and innovative composite materials are helping bring these qualities to the factory floor. Here, Robert Glass, head of marketing at global composite technology company, Exel Composites, explores how composite components can enhance the performance of automated machinery.
Improving manufacturing efficiency while maintaining high product quality is a common challenge in production facilities. Automation has undoubtably boosted productivity, but rising consumer demands drive a need to further optimize production equipment. By incorporating composite components into automated machinery, production speed and accuracy can be increased while reducing downtime.
As fast as you can
Composites, also known as fiber reinforced plastics, are fabricated by combining a resin matrix with reinforcement fibers. The blend of materials gives composites combined benefits, such as low weight with high strength and stiffness. In fact, composites have a specific gravity a quarter that of steel and two thirds of aluminum, and have a much higher strength-to-weight ratio.
This low weight gives composites the ability to move quickly, making them ideal for fast-moving machine parts. By using composite machine parts, which are lighter and stronger than their metal counterparts, the operation speed of a production machine can be increased, therefore increasing manufacturing efficiency.
This is especially true for textile machines. The textile industry must transform millions of miles of yarn into lengths of fabric to supply industries such as clothing and home furnishing. However, producing one length of fabric requires hundreds of weft yarns, making enhanced speed essential to keep up with demand.
In rapier weaving looms, finger-like carriers called rapiers repeatedly move the yarn back and forth across the width of the fabric. By using lightweight composite rapiers, as opposed to metal alternatives, the yarn placement process can be carried out faster and in greater volumes, therefore increasing fabric production efficiency. The high strength and durability of composites means the rapiers will be able to withstand working at the increased speed without breaking under greater force.
Process precision
Composites not only allow production machines to move with increased speed, but also higher accuracy. Composite materials have low inertia, which means composite machine parts can start movements and change speeds more quickly, therefore performing with increased agility.
The low weight and high stiffness properties of composites means they can provide vibration dampening up to 20 times better than steel. This increases the stability of the machine, allowing the composite component to perform with superior accuracy.
Composites also have a low coefficient of thermal expansion, so machine components will not change their dimensions even if the temperature rises or falls in the environment. By maintaining the dimensions, the composite components can keep machine operation to tight tolerances.
An application where agility is essential is robotics. Robotics on the production line must accurately maneuver products without causing damage. This is especially important when handling small, delicate products like electrical components or even chocolates in boxes. Here, by using carbon fiber for robotic arms instead of aluminum or steel, the arms can perform movements with quick changes in direction and high placement accuracy.
Reduced downtime
Composite machine components don’t just perform well — they perform for a long time. Composite materials exhibit high durability, meaning they require less maintenance and less frequent replacement, therefore reducing factory downtime.
Vibration dampening properties mean composite components display reduced wear from processing, as they are unlikely to experience cracking in applications with high levels of oscillation, and their resistance to fatigue means they can withstand repeated load cycles. Composites are also resistant to many external factors, such as chemicals, temperature and moisture.
Exel provides strong and lightweight composite solutions to the machine industry, from carbon fiber robot delta arms to textile machine parts. With over 60 years’ experience in engineering, we can work closely with customers to find a solution that is tailored to their unique project. This includes optimizing the properties of composites for a specific application by altering the fibers, matting and resin system. The speed and agility of cheetahs demonstrates the incredible design of the natural world, a source of inspiration for manufacturing. Composite components help advance automated machinery, making them perform with increased speed and precision, while also exhibiting extended durability.
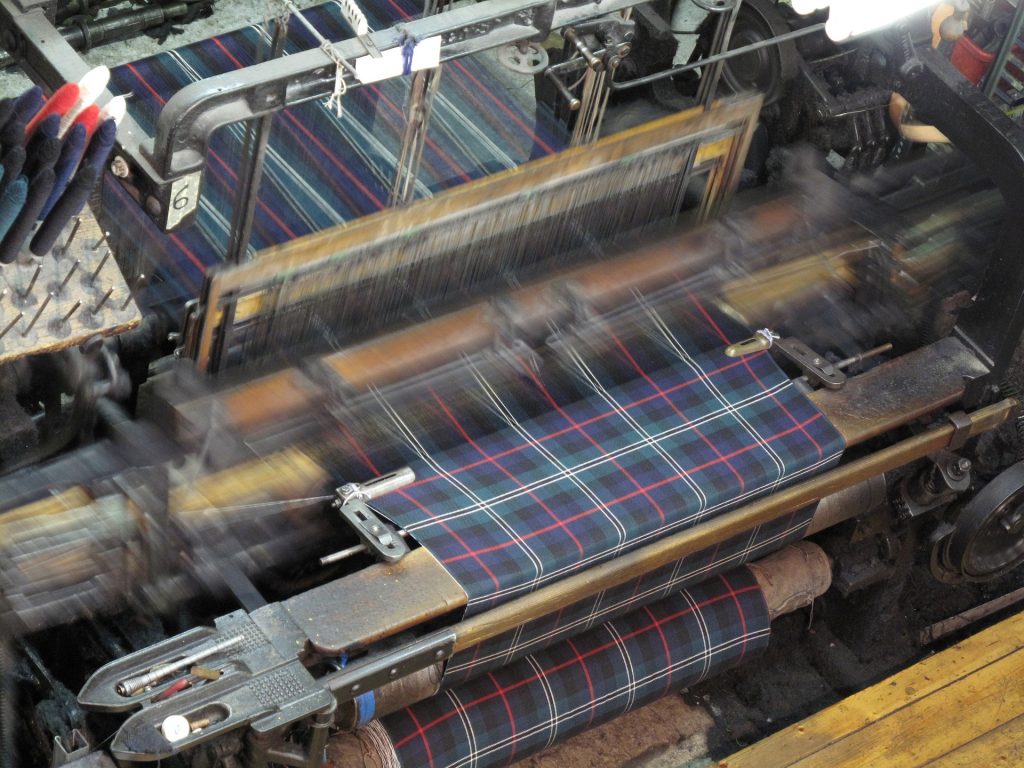