When lockdown triggered a huge surge in ecommerce orders, Pets at Home recognised the importance of upgrading the maintenance and support of its automated warehouse systems by outsourcing to Invar Integration. Maintaining uptime was critical to ensuring customers received their orders on time.
Pets at Home is the UK’s leading pet care business with over 450 stores and a growing ecommerce channel.
To keep pace with the increase of online sales, in 2019 the business took the decision to introduce an automated zone-picking operation at its Northampton DC, where miles of powered conveyor and a series of carton elevators smoothly transfer order-cartons over three floors of a mezzanine system.
Auto-carton erection and sealing machines work in unison with pickers in a 24/7 operation to complete some 15,000 parcels a day, comprising orders across a diverse 10,000 sku product range, from 25kg bags of pet food to a plethora of accessories, right down to a collar for a kitten. In addition, a further 8-9,000 daily orders for prescription medications are processed within a dedicated order assembly area.
Keeping such a highly mechanised fulfilment process running smoothly, with minimal failures or glitches, is absolutely critical to maintaining optimal performance and ultimately, ensuring customer satisfaction. Reliable on-site engineering support is, of course, essential.
When the pandemic hit, online demand surged due to lockdowns and travel restrictions, meaning there was a greater emphasis than ever to maintain performance.
Simon Phillips, General Manager at Pets at Home, explains: “Towards the end of 2019 we implemented our automated solution for ecommerce orders and then in early 2020 the pandemic suddenly struck, resulting in a huge shift to online sales.
“It was really fortuitous that we had made the decision to invest in automation when we did,” he says. “That decision wasn’t driven by capacity issues at the time, but subsequently it has allowed us to meet the phenomenal surge in demand resulting from lockdown.”
He adds: “We have seen volumes through our online channel more than double over the last year, whilst at the same time the business is going through significant double-digit growth.
As a consequence, we soon realised that we needed to increase our engineering support rapidly to maintain performance.”
To address these challenges, Pets at Home turned to warehouse automation specialists, Invar Integration, for an outsourced maintenance solution. In the spring of 2020 Invar was engaged to provide a professional team of four on-site engineers with a remit to manage a 24/7, 364 day a year service, offering a planned preventative maintenance programme, immediate failure resolution, spare parts inventory management and further back-up support – tapping into the full technical capabilities and resources of the Invar Group. As online sales boomed, it wasn’t long before Invar Integration expanded the team to five by bringing on board a full-time onsite manager to co-ordinate resources.
Invar Integration was tasked with ensuring maximum uptime with little room for failure.
A strict set of SLAs was put in place to track performance month by month: Overall availability of the system has a KPI target of 96%, scanner read rates 98%, recommended spares held vs recorded spares 98%, planned maintenance vs completed maintenance 97% and engineering shifts completed and fulfilled 99.8%.
Alex Moore, Maintenance Contract Manager at Invar Integration, says: “It’s an extremely busy warehouse. We have a full preventative maintenance schedule in place spanning 52 weeks of the year, involving in-depth checks across the system, identifying and replacing components close to failure, such as drive motors, rollers or worn drive bands. And this extends right across the entire system, including the carton erectors and packing machines.
“An important aspect of our work is the provision of spares – we plan what parts to hold in stock and manage the inventory, which is vital for ensuring maximum uptime of the system,” he says.
Invar Integration’s IT systems are used to manage parts holding, directly linking into the planned preventative maintenance schedule.
Simon Phillips explains how this has delivered significant benefits: “Invar has been really great at helping us determine what the planned preventative schedule needs to look like under this increased pressure, what spare parts we need to hold, and when we need to take the equipment down to provide a window of opportunity for planned maintenance – this has probably been the biggest learning curve for us, and has allowed us to significantly increase the reliability of the system.”
Of course, system performance is particularly critical at peak periods. “We have the retail Christmas peak,” he says. “During this period we see a good 30-50% uplift in volume and I’m happy to say that the modelled and planned maintenance and support structure put in place by Invar copes well.”
Phillips points out: “The last 12 months has seen a really big shake-down of what we would describe as a new system, so there have been some challenges to overcome. However, we have been able to utilise Invar’s industry expertise and network to resolve these pretty quickly. For instance, we had a failure on a carousel that lifts cartons up from the ground floor to the mezzanine floors, but Invar had it back up and running within a matter of hours.”
A full understanding of the many varied forms of warehouse automation is essential for any business offering a comprehensive maintenance and support service. Being a well established systems integrator helps. “Invar has been very supportive in bringing new ideas to the table, says Simon Phillips. “They have been great at listening to us, and in trying to understand our business. We have a fantastic working relationship with them and importantly, they deliver what they said they will deliver – and that has stood them in very good stead.”
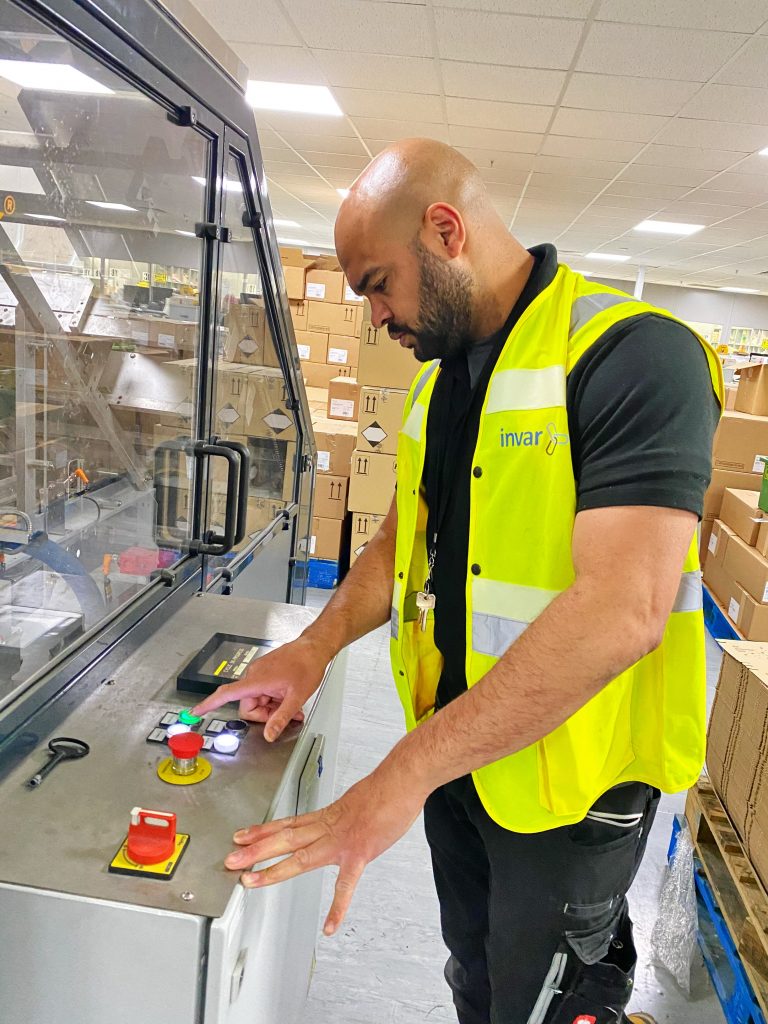
More information on Invar Integration’s contract maintenance services at www. invarsystems.com