Founded at the height of the pandemic in September 2020, AXI5 Ltd is a subcontract company that manufactures high-end bespoke components for the motorsport, oil, gas and press tool industries as well as designing and producing specialist tooling and toolholders. The company set itself up for success from the start with the purchase of a Mazak Integrex i-100 5-axis multi-tasking mill/turn centre, a Hurco VM10i machining centre, hyperMILL CAM software from OPEN MIND Technologies and cutting tools from Tamworth specialists Industrial Tooling Corporation (ITC).
Immediately investing in the latest CNC machine tool technology, a high-end CAM system and industry-leading cutting tools from ITC, the Southam-based company has made a phenomenal start in its first two years of business. Like any business, the support of supply chain partners can be instrumental to success, and AXI5 has recognised this on numerous occasions where ITC has supported the fledgling business with everything from ITC Widia VariMill end mills, general purpose Widia Hanita end mills, the Widia VDS drills and ITC’s extensive range of threadmills. When the small business was having challenges machining a series of high end components, it was ITC’s Application Engineer Simon Yeomans was on hand to support the company.
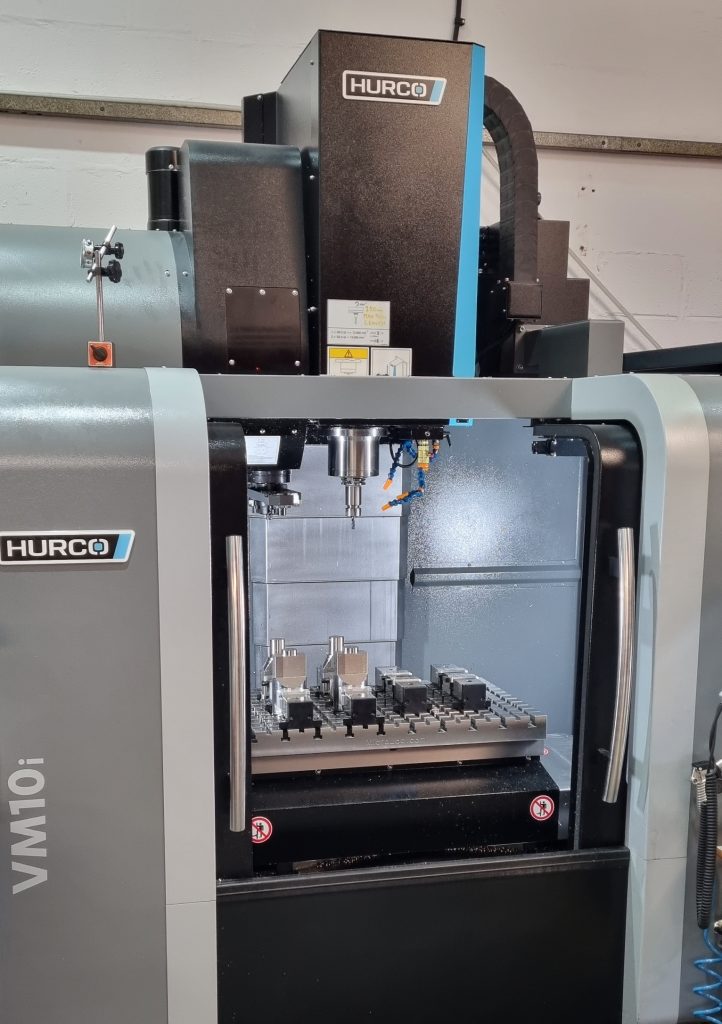
With demand for regular batches of 50 to 100-off parts for a prominent company, AXI5 was having issues with its cutting tool performance. With the project expected to be an ongoing regular commitment from the customer – a solution was needed. So, AXI5 called upon ITC to solve the problem. On its compact Hurco VMC, the Warwickshire manufacturer set up two Microloc clamping systems to machine 100mm diameter billets that are 92mm long. The set-up was clamping on 15mm of stock with a bar protrusion of 77mm.
Despite the robust performance of the Microloc system, rough machining a square profile in the round billets created excessive noise and didn’t give the AXI5 team the confidence to leave the machine to run through its cycle. As well as creating excessive noise, the 25mm diameter indexable end mill was also providing limited tool life and poor material removal rates. Investigating the process, ITC’s Simon Yeomans recommended the Widia VXF high-feed 52mm diameter face mill with five insert seats for the rough machining of the parts.
With two parts clamped on the machine and milled in a single operation, the previous cycle time with a rival tool was 15 minutes, something that ITC rapidly cut to just under nine minutes – a 40% cycle time-saving. This was achieved by executing cutting parameters of 163m/min with 0.75fz and 0.8ap with a ramp angle of 0.7°. The result was that the 15-5PH stainless steel parts that had been annealed to BM9050 and were proving a particular challenge – had been overcome by ITC with a significant productivity increase.
The key challenge for AXI5 was having the confidence to walk away from a process that was creating excessive noise. Thankfully, the smooth cutting action of the Widia VXF high-feed face mill eliminated excessive noise and chatter and gave the small business confidence to allow the machine to run unattended. The impressive cutting characteristics of the ITC Widia VXF tool also delivered reduced costs and prolonged tool life.
With two parts clamped in the work envelope simultaneously, AXI5 could only machine four parts before an insert change was required with the previous tool. However, the ITC Widia VXF could machine three batches of parts as opposed to two – 6 parts instead of 4. This impressive performance on a particularly difficult material equated to one hour of machining time for each insert edge with the Widia VXF face mill. Equally impressive is the ability of the new ITC Widia tool to reduce costs for the business. On a run of just 600 parts, ITC is expected to save AXI5 over £4000 – or £6.60 per part.
As a company utilising the latest machine tool technology to machine a wide range of materials that stretches from steel and stainless to titanium and nickel and chromium-based superalloys – the journey with ITC is just getting started and the cost savings and productivity improvements will continue to follow.
Discussing the relationship with ITC, Production Director and Co-owner Dave Wear says: “We have known the ITC team from previous roles with other businesses and their support and products have always been outstanding. So, when we set up our own business, ITC was one of the first companies we called. They are a UK manufacturer, which means they hold stock of thousands of items and provide next-day delivery. This is not often the case with overseas manufacturers. The pricing structure is clear and concise and we also utilise the re-grind service. As a small business in the early stages of growth, having a re-grind service to minimise our costs and waste is of critical importance to us. Our next step will be to have a consignment stock of ITC products.”
“The product quality is second to none and we have improved tool life and cycle times over and again with the Widia range from ITC. The ITC threadmills that are manufactured in the UK are also giving us 3-times tool life improvements when compared to previous products. We have outstanding support, friendly advice, an unfathomably wide choice of products, industry-leading performance and the majority of tools are manufactured in the UK – what more could a manufacturer want from its cutting tool supplier. Our next move will be to organise a consignment stock for our ITC tools,” concludes Dave.