ATL Technology in Cardiff is a specialist manufacturer of medical devices, particularly energy-driven surgical devices. These are used in minimally invasive surgery and use low voltage, high current RF energy waveforms to seal, coagulate, dissect, vaporize, resect, or mobilize tissue. Typical applications are in urology, gynaecology, and arthroscopy.
As a company committed to delivering tailored products for specific medical applications, ATL Technology collaborates closely with surgeons throughout the design and production process. To ensure rapid development and timely completion of projects, continuous prototyping plays a crucial role. This approach is essential due to the stringent requirements for quality, repeatability, reliability, and cleanliness inherent in medical device development.
ATL Technology in Cardiff utilises two toolrooms to produce prototyping tooling, jigs, fixtures for production, specialized in-house machinery for assembly and disassembly, and spare parts to maintain the special-purpose production assembly line.
The Research and Development toolroom initially adopted the XYZ SMX 2500 bed milling machine in 1997. Over time, its capabilities have expanded with the addition of a 660 HD vertical machining centre, a 1340 lathe, and an XYZ 500 LR vertical machining centre featuring linear rail technology.
Meanwhile, the Maintenance toolroom utilizes an RLX 1630 lathe, an XYZ 1500 manual turret mill, and an XYZ RMX 2-OP, which specializes in machining light alloy and plastic parts from stock materials. The recent acquisition of an XYZ 500 TMC in March 2023 further highlights ATL Technology’s longstanding investment in XYZ machines.
Stephen Green, Process Development Engineer, highlights the advantages of the XYZ 500 TMC, stating,
“The XYZ 500 TMC has a larger working area. This enables us to machine bigger mould tools, jigs, and fixtures in-house, which we were previously subcontracting. It has more power, a 12k spindle—which is ideal for small tools—and through tool coolant. This makes it easy to machine tool steels for injection mould tooling and electrodes for die sinking. It is also good at deep hole drilling, delivering faster material removal rates. With subcontracting, it took many weeks to deliver a tool. Now we can produce an entire tool within a week, or a single part to repair a production line breakdown within 24 hours.”
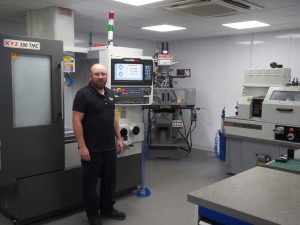
For ATL Technology, the ability to rapidly produce prototype parts—using metal injection moulding sintering techniques from 17PH powder with an ABS substrate—is crucial. The quick iteration and lifecycle testing of prototypes play a significant role in refining product designs to meet the specific requirements of health professionals while ensuring manufacturability.
The XYZ 500 TMC’s ProtoTRAK® control provides ATL Technology’s engineers with a convenient way to program parts directly in the workshop. Additionally, CNC programs for prototype parts are mostly generated offline in Autodesk FeatureCAM from CAD models supplied by the Product Development team. The ProtoTRAK® control allows engineers to verify the program, enabling them to review and correct any errors before machining begins.
Ashley Gardiner, Toolroom Technician, emphasizes the machine’s versatility, stating,
“90% of our work is one-off, small batches or spares, and the 12 tool pockets on the 500 TMC are sufficient for most of our needs. With this machine, we have increased our capacity to rapidly develop new devices and keep our production lines operating. Generally, we are looking for ±50 microns. With the TMC, we can achieve ±10 microns and, using the probe on the machine, we can also do in-process checking to ensure the part is correct before we take it off.”
To accommodate the XYZ 500 TMC in the Maintenance Toolroom, XYZ Machine Tools had to dismantle the machine entirely to fit it through the door. The technicians from XYZ Machine Tools then meticulously reassembled and tested the machine to ensure its functionality, accuracy, and reliability. Overall, the machine’s adaptability and XYZ Machine Tools’ reliability have made the partnership invaluable to ATL Technology.
In conclusion, the integration of the XYZ 500 TMC has significantly enhanced ATL Technology’s medical device development capabilities. The ability to rapidly prototype, create specialized components in-house, and achieve high precision has allowed ATL Technology to stay at the forefront of medical device innovation, ensuring the delivery of cutting-edge products to meet the needs of healthcare professionals.